This month, Angelos goes through what a typical day for him looks like...
Having a set, daily schedule is a very interesting “concept” in someone’s life, at least in my opinion. Waking up at a set time and taking the correct means of transport, to be on time for work, can be challenging, especially if it’s compared to our previous lifestyle, in the University.
In “Uni”, as students like to call it, we normally wake up 20-30 minutes before the lecture (no matter the time), get dressed, and walk to the campus. If you live next to the campus, just like I used to, the whole process needs less stress, as you will need 5-10 minutes, instead. In Uni, we spend a couple of hours around campus, going from lecture halls to labs, and from the coffee shop to the library, and after all is done, we go out, or to our friend’s house, to” relax and take a breather”. Every student needs to relax after a hard day and all this walking around, and, let’s be honest, no one studies anything Uni-related, after Uni, unless it’s the exam period (you should study though, studying is good). The overall lifestyle is relaxed, with some ups and downs here and there, but now, the “Placement lifestyle” is very different.
Traveling to your placement
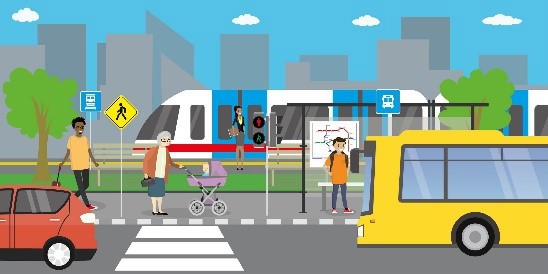
As I said before, you will have to commute, because no one lives, or would like to live, next to their workplace. If you drive and you have a car, that’s great, but if you drive but you don’t have a car, like me, life gets hard, and even harder the farther you live.
Personally, I have to take a train, a bus, and walk a bit, to get to work. It is not as bad as it sounds, it’s a total of 30 minutes travelling, 10-15 minutes of waiting and 10 minutes of walking (enough exercise for a day, considering I have to do this twice a day, adding an extra 10-minute walking distance from my home to the station). All this travelling wakes me up too, so I do not mind at all, especially when I have my headphones on. So, after 40-45 minutes, I arrive to Mi3, ready to scan myself in using my fingerprint, because technology and automation are amazing.
Daily life
Now, let’s jump into my perspective and point-of-view. I am in, scanned through the door, feeling like a secret agent entering his underground office, and now it’s time to go to my desk. Yes, I have my own desk. Nothing fancy or super private, there is the “open door” policy in this company after all, but it is still decent and spacious enough for me. It is time to stick to the 1-2-3 rule (I made that up since starting).
- Turn the computer on and log in
- Get your agenda/diary/weekly planning notebook and a pen
- Open your emails
Emails and your agenda are your best friends during your placement. That is because everything that happens will be either sent through via email, or in person, so always carry your agenda.
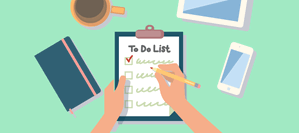
After I check my emails and identify the updates regarding previous tasks, I dive into my personal work schedule. In there, I write all the tasks I have to do, and categorise them by “Due Date”. Doing so, helps me keep track of my progress on all of my projects and tasks, and makes sure that I complete everything on time. Thus, I pick the most critical deadlines and work on those tasks for the day.
For today, I have to do a couple of things, starting off with “Specifications Updates”. For that, I should find out more about the new material that is going to replace the material we currently use for 5 components. It is not that hard. I have already emailed the supplier to give me the “Technical Data Sheet” and the “Safety Data Sheet”, so I can now do the “fun” part. I need to find the material the supplier uses, replace it in the old “Product Specifications” document, add a few details here and there, replace the safety procedure, which gives an overview of how to handle this material, and after all the changes are made, I can print the new document, together with an approval form, and give it to my line manager for review. When he reviews it, I will go around the office, give it to the corresponding managers for review, and if they are happy and sign it, I can then publish it in the QMS (Quality Management System) folder as a “Live Document”. Paperwork. I know… I don’t enjoy it either, but it is necessary for medical devices, so I must not avoid it.
Task number 2 is… CAD (Computer Aided Design)! Great! That’s a job for an engineer, right? So, what do we have here? Design this part for that product, based on the customer’s specifications… OK, I can do that! I will open Solidworks, pick a plane, click Sketch, and start drawing. You know the drill.
Ok, it’s been 2 hours, since I started it and I think it’s done. My line manager approved it, so it is ready to… Oops! Forgot to make the drawing. That does not take time. A few clicks here and there, put those views, some measurements, update the table, print it... Done! Easy! Time to make my second tea. Hydration is a very important. Also, don’t forget to stand up occasionally and take a breather, it is very important and encouraged, especially by the HSE (Health, Safety and Environment) department.
Task number 3: 3D Print the prototypes I designed yesterday. I really like doing that.
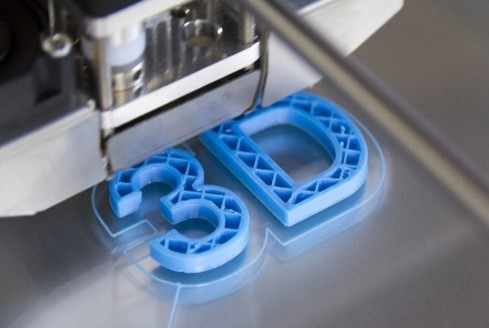
I believe 3D printers are amazing. First things first, I need to slice the CAD models and make the appropriate settings so that the 3D printer will be able to... print them. I will change the material from Nylon to PLA (its more environmentally friendly), and will remove the support material, as I don’t need it. Ok, click slice… 4 hours of printing. Not too bad. I need to set the 3D printer up now as well. Following the Work Instructions, I need to remove the old material, put the new one, and press start printing. Ready! See you in 4 hours. Setting up the 3D printer takes me around 30 minutes, depending on the speed that the 3D printer warms up and the time it takes to calibrate the building plate. Sometimes it’s a hassle but, I like it.
Task number 4… Meetings! So, in 10 minutes I need to attend an online call with a FEA (Finite Element Analysis) company, for some parts that we need to assess. It normally takes 30 minutes which is not too bad, but, after that, I need to run to a meeting room for a small meeting with my Line Manger. I can do that.
So, the meeting with the FEA company went well, they understood what we need and after giving them the materials of each component, they can do the analysis and hopefully by next week, we will have the results and conduct a report for the clients. That is next week’s task then, which I should now write down. Don’t forget to fill in the agenda. In 5 minutes, I have the meeting with my Line Manager. It is a 1-to-1 meeting that we have every week, in which we talk about the workload of the week, how I am doing with the tasks, what’s next, and an overview of how I find it so far in the company; Busy, but Good Busy!
What’s next, what’s next… Oh… Lunch Break! Best time of the day. Those 30 minutes off, are very helpful to relax and forget work for a couple of minutes.
I am back. Task 5: Measurements in the cleanroom.
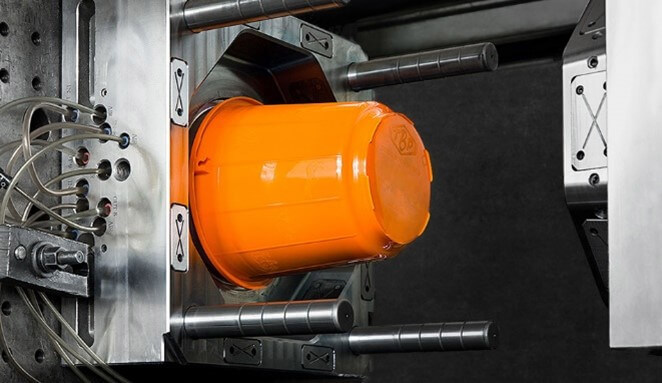
That’s a very nice task, because I am working with another placement student. Firstly, we need to change. Put on a hairnet before getting in the changeroom, clean our hands, wear our “Tyvek Coveralls” and gloves, and get in the cleanroom. Time to work. We are measuring each component that came from the Injection Moulder and write our results down. Then I will put all these results in an “Excel” sheet and do data analysis, so we can find out, which are the best settings for injection moulding those specific parts. That will take us around 2 hours.
Measuring is done! It’s been two and half hours, but it was worth it. We measured everything and now, I will go to my desk, put the data in, analyse them and send them to one of our line managers, who is responsible for the whole project.
Ok, I input the data and did the data analysis I had to do. It was not very hard, more time consuming than hard, I’d say. What’s left…oh wow, it’s 16:10, almost time to go. I will quickly fill my agenda with the last task I did, write them on my work schedule, so tomorrow I will be sure that they are done. Also, a quick check on my emails. Nothing special, as it seems, it was a quiet day.
Time to head off! Bye-Bye, everyone, see you tomorrow. Oh yeah, tomorrow is Friday! Shorter day, breakfast in the office and hopefully a sunny/warm day. Also, I have less tasks, considering that I did a lot today, but there is always a chance for a new surprise.
Final thoughts
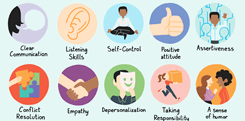
As I said before, “work lifestyle” is far different than “Uni lifestyle”. It is more arranged and fuller, but it helps you get accustomed to it, as in your future career, you will have similar schedules. That is the reason I am enjoying is so much at Mi3. Although there are drawbacks (waking up early, traveling, working hard, the advantages and the things you do, outweigh them by far. Finally, you practise and improve your own skillset daily, but you also learn a lot of new things and develop new skills, that will help you further on your future career and life. Skills like teamwork, time management, socialising and “networking” are some of those. The rest… You will identify them on your placement.
About the author - Angelos Stavropoulos – Angelos is a third-year student at the University of Bradford, studying Biomedical Engineering and is interested in Prosthetics and Tissue engineering, hoping to use the year in industry at Mi3 to further develop existing skills, apply his knowledge in practise and understand in depth the medical field, from a manufacturing perspective. Following his placement at Mi3, Angelos will return to Bradford to progress with his studies, doing a Master’s in Biomedical Engineering